OIL & GAS
Re-tubing/Tube Replacement
Re-Tubing / Tube Replacement: Essential Re-Tubing Services for Heat Exchangers, Condensers, and Boilers in the Oil and Gas Industry
Re-tubing, or tube replacement, is a crucial maintenance service in the oil and gas sector, particularly for heat exchangers, condensers, and boilers. Tubes often face corrosion, erosion, and scaling due to harsh operating environments characterized by extreme temperatures and corrosive fluids, coupled with mechanical wear from high pressure. Neglecting to repair degraded tubes can lead to leaks, reduced efficiency, and costly unplanned shutdowns.
Our re-tubing services involve the removal or replacement of damaged tubes with new ones, restoring the optimal performance of your equipment. This process not only ensures safe operation and enhances heat transfer efficiency but also extends the life cycle of critical assets. Additionally, it helps facilities comply with regulatory standards, mitigating the environmental risks associated with leaks or system failures.
By proactively scheduling tube replacements, companies can prevent catastrophic failures, achieve significant energy savings, and enhance overall productivity. We also utilize advanced materials in the re-tubing process, which increases resistance to future wear and promotes long-term operational reliability.
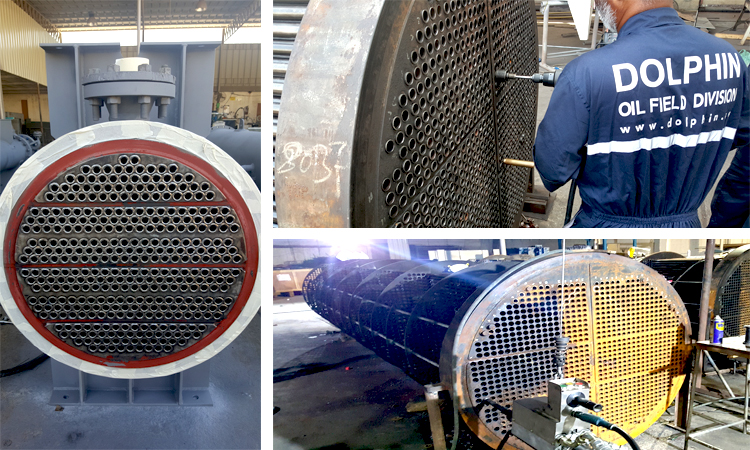
FEATURED
Why Choose Us?
We deliver high-quality, durable, and customizable solutions for radiators, coolers, and HVAC systems across various industries. With expertise, innovative designs, and a commitment to excellence, we ensure optimal performance, reliability, and efficiency for all your cooling needs.
Dedicated Team
True Partners
Global Know-How
Focus On Innovation
PROJECT
Projects in the field
Heat Exchangers
We successfully refurbished 16 seal oil coolers, which included replacing tubes and overhauling 3-way valves. Each cooler was tested at a pressure of 90 bar, and we applied a specialized anti-corrosive coating on the tube sheet to enhance durability and performance.
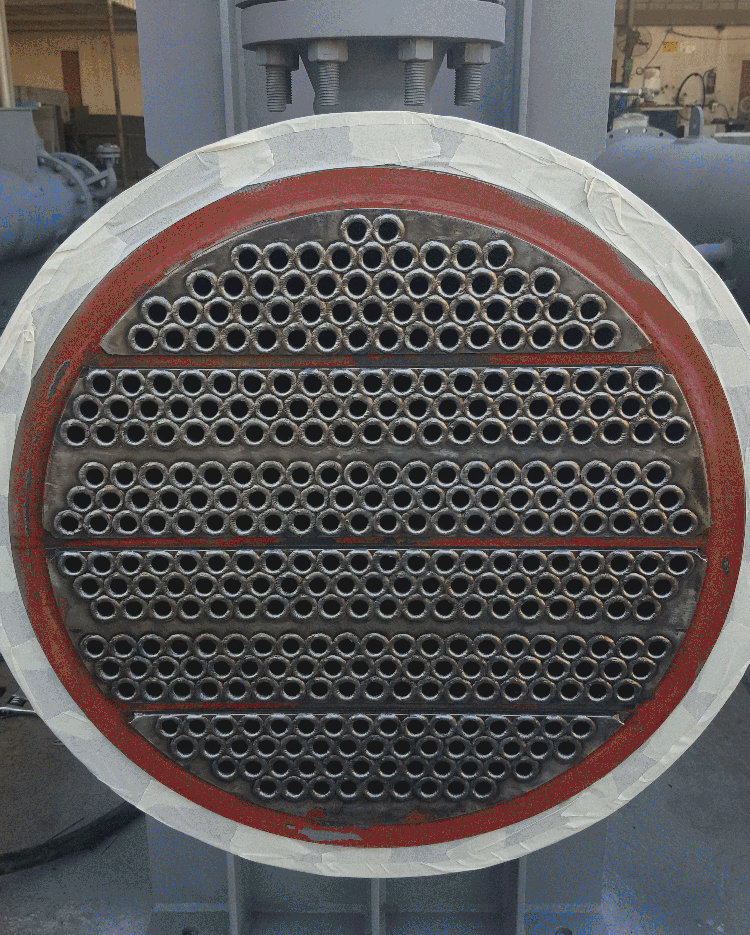
Retubing
We executed a heat exchanger tube bundle replacement project for the Main Column Trim Condenser during a refinery shutdown. This involves replacing 12 bundles, each with 1,060 CuNi 70/10 tubes, with a completion timeline of 4 weeks. Our goal is to boost efficiency and reliability while minimizing downtime.
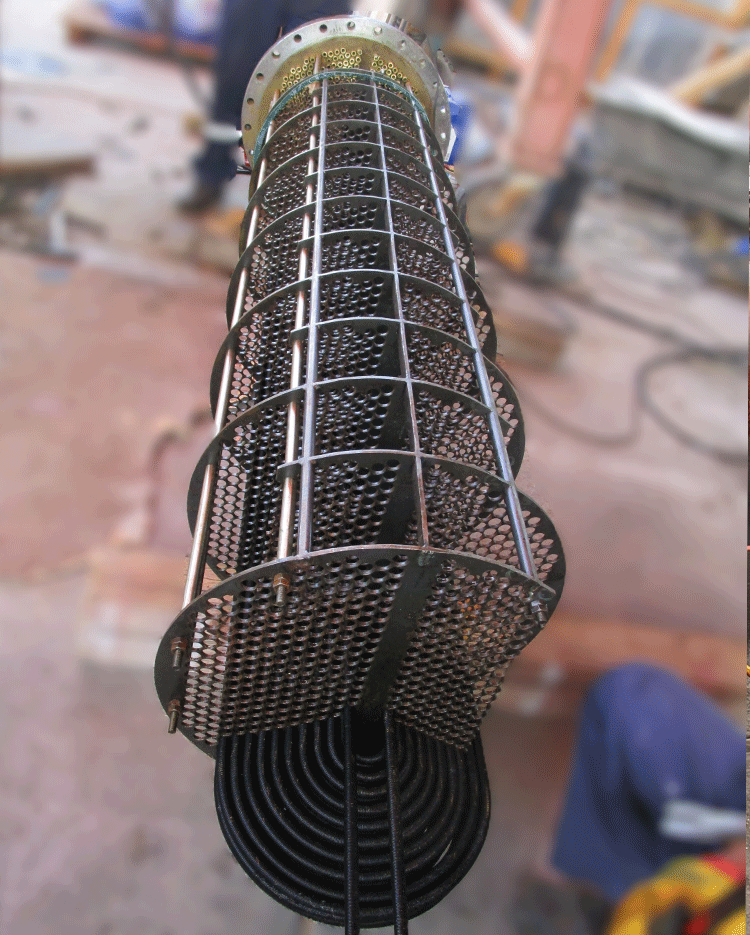