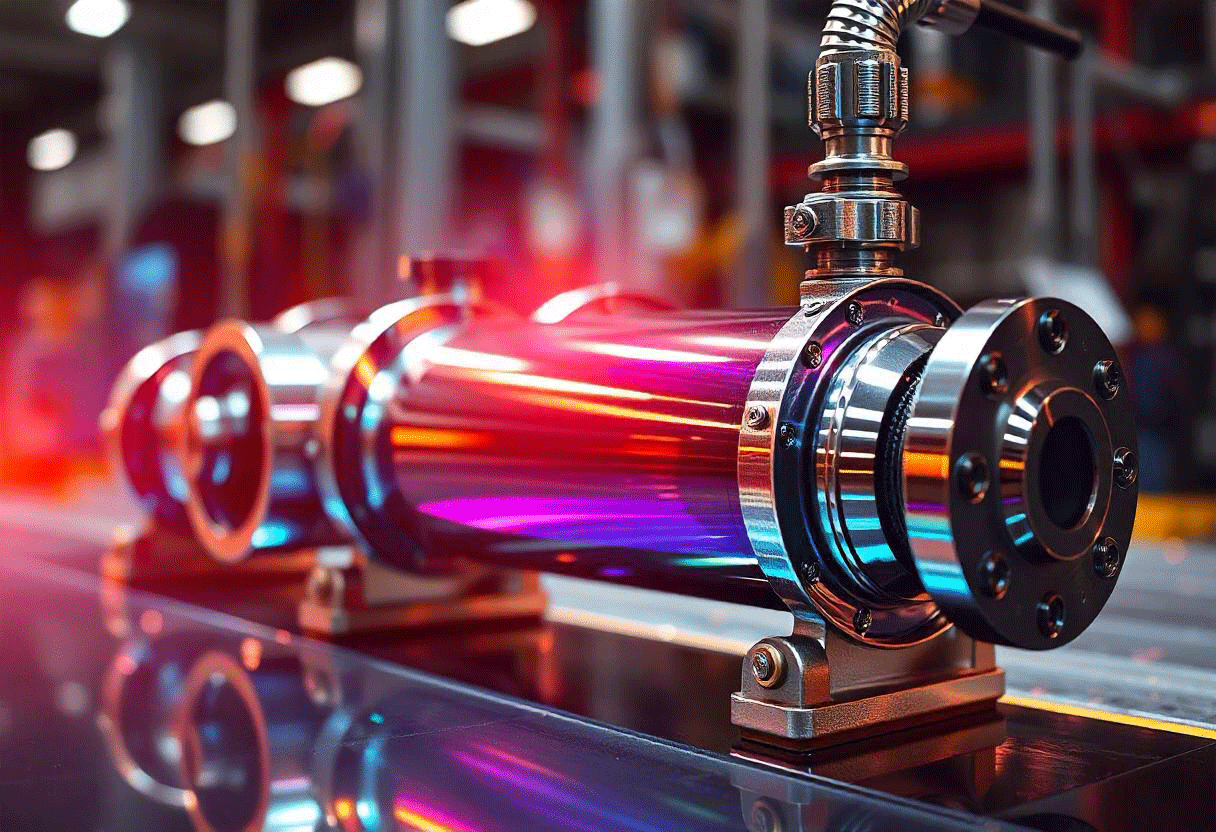
Revolutionizing Manufacturing with AI: The Digital Twin Model
One of the most transformative innovations is the concept of the digital twin. This technology, particularly in the context of heat exchangers and cooling systems, is revolutionizing the way manufacturers approach design, maintenance, and operational efficiency.
What is a Digital Twin?
A digital twin is a virtual replica of a physical asset, process, or system. It uses real-time data to simulate the performance and behavior of its physical counterpart. In manufacturing, digital twins allow companies to monitor, analyze, and optimize their equipment and processes without the need for physical intervention. This technology is particularly beneficial for complex systems like heat exchangers, where precise performance metrics are crucial for efficiency and reliability.
Applications in Manufacturing
In the realm of heat exchangers and cooling systems, digital twins provide invaluable insights. By creating a digital model of these systems, manufacturers can simulate various operating conditions and assess how changes in design or operation affect performance. This capability is essential for optimizing heat exchanger design, ensuring that systems operate at peak efficiency.
This technology is particularly beneficial for complex systems like heat exchangers, where precise performance metrics are crucial for efficiency and reliability.
Benefits of AI Integration
Integrating AI with digital twin technology enhances its capabilities significantly. Here are some key benefits:
- Predictive Maintenance: AI algorithms can analyze data from the digital twin to predict when maintenance is needed, reducing unexpected downtime. For instance, by monitoring temperature and pressure data, manufacturers can identify potential failures before they occur, allowing for timely interventions that minimize disruption.
- Design Optimization: The digital twin enables manufacturers to experiment with different design configurations in a virtual environment. By simulating various scenarios, engineers can identify the most efficient designs for heat exchangers and cooling systems, leading to improved performance and reduced energy consumption.

- Operational Efficiency: Real-time monitoring through digital twins allows for continuous performance assessment. Manufacturers can quickly identify inefficiencies and implement corrective actions, leading to enhanced productivity and reduced operational costs.
Enhancing Service Offerings
The adoption of digital twin technology not only improves internal operations but also enhances customer service. With a digital twin, manufacturers can offer clients real-time insights into system performance and maintenance needs. This transparency builds trust and allows for proactive communication, ensuring that customers are always informed about their systems’ status.
Moreover, the ability to simulate various operational scenarios means that manufacturers can provide tailored recommendations for optimizing system performance based on specific client requirements. This level of customization enhances customer satisfaction and fosters long-term relationships.
Conclusion
The digital twin model, powered by AI, is revolutionizing manufacturing, particularly in the context of heat exchangers and cooling systems. By providing a virtual representation of physical assets, manufacturers can enhance predictive maintenance, optimize designs, and improve operational efficiency. As industries continue to embrace this technology, the potential for increased productivity and customer satisfaction will only grow.