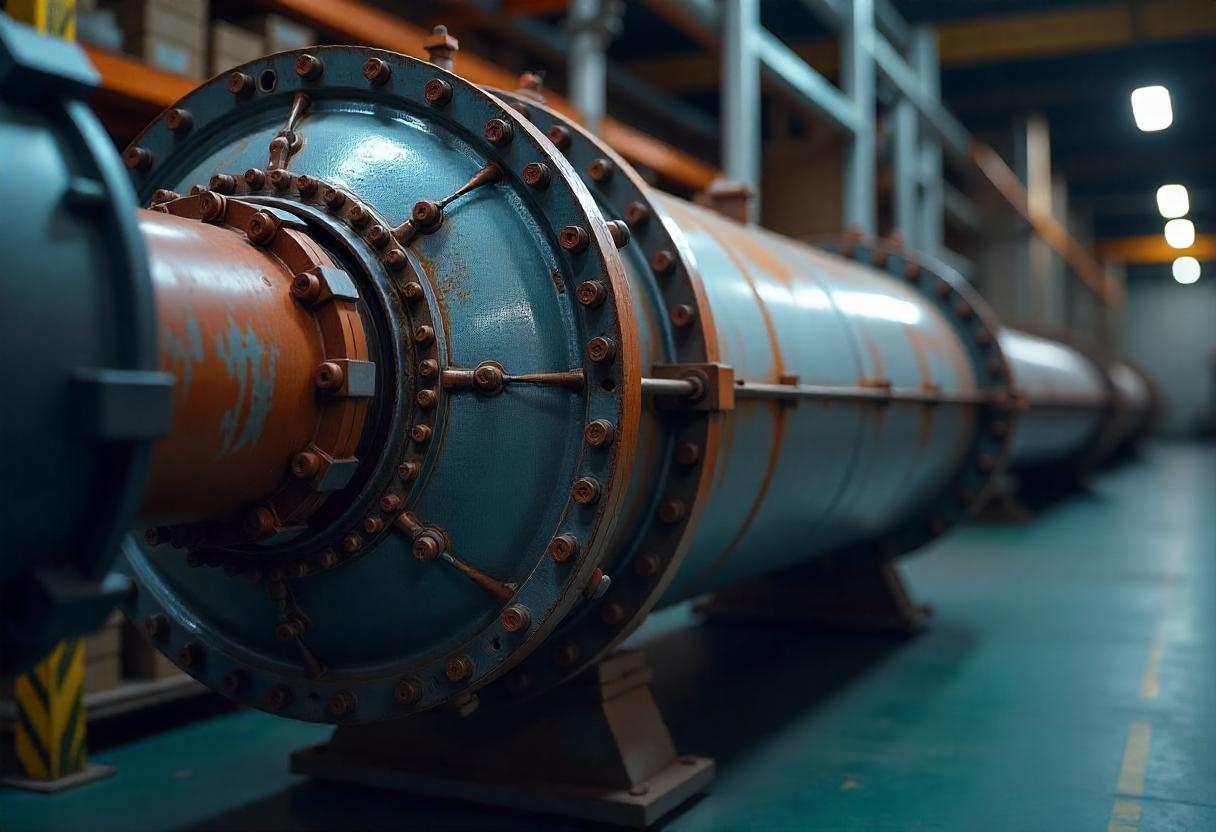
The Essential Role of Heat Exchangers in Modern Industry
Heat exchangers play a crucial role in ensuring efficient thermal management across various applications. From automotive cooling systems to HVAC installations, these devices facilitate the transfer of heat between fluids, making them indispensable in maintaining optimal operating conditions. This blog delves into the various types of heat exchangers, their applications, and the manufacturing processes involved, while highlighting the importance of quality and customization in meeting specific client needs.
Understanding Heat Exchangers
Heat exchangers are devices designed to transfer heat from one medium to another without mixing them. They are vital in numerous sectors, including automotive, HVAC, chemical processing, and power generation. The efficiency of these systems significantly impacts overall operational performance, making their design and manufacturing processes critical.
From automotive cooling systems to HVAC installations, these devices facilitate the transfer of heat between fluids, making them indispensable in maintaining optimal operating conditions.
Types of Heat Exchangers
- Shell and Tube Heat Exchangers: One of the most common types, shell and tube heat exchangers consist of a series of tubes, with one set carrying the hot fluid and another the cold fluid. Their robust design allows them to handle high pressures and temperatures, making them suitable for various industrial applications, including oil refineries and chemical plants.
- Plate Heat Exchangers: These compact devices utilize a series of thin plates to facilitate heat transfer. The design maximizes surface area while minimizing space, making plate heat exchangers ideal for applications where space is at a premium, such as in food processing and pharmaceuticals.
- Air Coolers and Fin Fan Coolers: These systems use ambient air to cool fluids, making them energy-efficient options in industrial settings. Air coolers are commonly used in power plants, while fin fan coolers are prevalent in oil and gas applications.
- Finned Tube Heat Exchangers: Featuring extended surfaces, finned tube heat exchangers enhance heat transfer efficiency. They are often used in HVAC systems and industrial processes where air or gas needs to be cooled or heated.
Applications Across Industries
The versatility of heat exchangers allows them to be utilized across various industries:
- Automotive: In vehicles, heat exchangers are essential for engine cooling and cabin climate control. Custom designs can optimize performance, ensuring that vehicles operate efficiently under varying conditions.
- HVAC: In heating, ventilation, and air conditioning systems, heat exchangers regulate indoor temperatures, contributing to energy efficiency and comfort in residential and commercial buildings.
- Chemical Processing: Heat exchangers are pivotal in chemical reactors, helping to maintain optimal temperatures for reactions and ensuring product quality.
Manufacturing Processes
The manufacturing of heat exchangers involves several critical steps:
- Design and Engineering: The process begins with detailed design and engineering, where factors such as heat transfer requirements, fluid properties, and space constraints are considered. Advanced software tools are often used to simulate performance and optimize designs.
- Material Selection: Choosing the right materials is crucial for durability and efficiency. Common materials include stainless steel, copper, and aluminum, each selected based on the specific application and operating conditions.
- Fabrication: The fabrication process involves cutting, welding, and assembling components. Precision is key here, as even minor deviations can impact performance. For instance, adhering to standards such as ASME Sec VIII ensures that pressure vessels and heat exchangers meet safety and quality requirements.
- Testing and Quality Assurance: After fabrication, heat exchangers undergo rigorous testing to ensure they meet performance specifications. This may include pressure testing, leak testing, and thermal performance evaluations.
The manufacturing process involves careful design, material selection, fabrication, and testing to ensure quality and performance.
Importance of Quality and Customization
Quality and customization are paramount in heat exchanger manufacturing. Off-the-shelf solutions may not meet the specific needs of every application, leading to inefficiencies and potential failures. Custom designs allow manufacturers to tailor heat exchangers to exact specifications, ensuring optimal performance and longevity.
For example, a manufacturer might work with a client in the oil and gas industry to design a heat exchanger that can withstand corrosive fluids and high temperatures. By utilizing advanced materials and engineering techniques, the manufacturer can deliver a solution that enhances operational efficiency and reduces maintenance costs.
Key Takeaways
- Versatility: Heat exchangers are indispensable in various industries, including automotive, HVAC, and chemical processing.
- Types: Different types of heat exchangers, such as shell and tube, plate, and finned tube, serve specific applications based on their design and efficiency.
- Manufacturing: The manufacturing process involves careful design, material selection, fabrication, and testing to ensure quality and performance.
- Customization: Tailored solutions are essential for meeting specific client needs, enhancing efficiency, and prolonging equipment lifespan.
By understanding the essential role of heat exchangers and the processes involved in their manufacturing, industries can better appreciate the importance of investing in quality solutions that meet their unique operational demands.