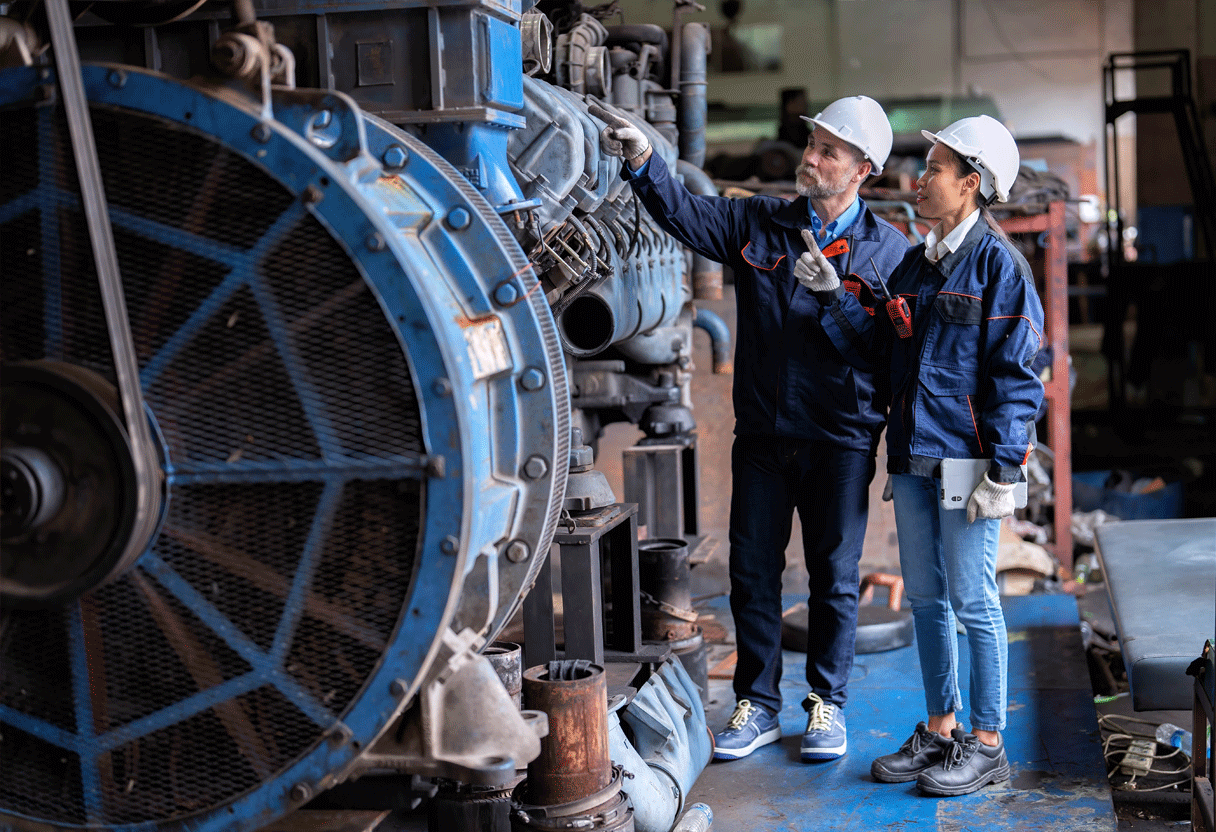
The Importance of Custom Radiator Solutions for Automotive and Industrial Applications
In today’s fast-paced industrial and automotive sectors, the efficiency and reliability of cooling systems are paramount. Custom radiator solutions play a crucial role in ensuring optimal performance, particularly in environments that demand high levels of precision and reliability. From automotive applications to large-scale industrial processes, tailored radiator designs can significantly impact operational efficiency, maintenance costs, and overall system longevity.
Heat exchanger manufacturing involves intricate design and engineering processes to create units that meet stringent standards, such as ASME Sec VIII, which governs the design and fabrication of pressure vessels and heat exchangers.
Understanding Custom Radiator Solutions:
Custom radiator solutions are specifically designed to meet the unique requirements of various applications. Unlike standard radiators, which may not adequately address specific operational needs, custom solutions consider factors such as heat load, fluid type, and environmental conditions. This tailored approach ensures that the radiator operates efficiently, reducing the risk of overheating and extending the life of the equipment.
Heat Exchangers Manufacturing: A Key Component
At the heart of many cooling systems are heat exchangers. These devices facilitate heat transfer between two or more fluids, which is vital in maintaining optimal temperatures in both automotive and industrial applications. Heat exchanger manufacturing involves intricate design and engineering processes to create units that meet stringent standards, such as ASME Sec VIII, which governs the design and fabrication of pressure vessels and heat exchangers.
Types of Heat Exchangers
Several types of heat exchangers are commonly used in custom radiator solutions:
- Shell and Tube Heat Exchangers: This design consists of a series of tubes, one set carrying the hot fluid and the other the cold fluid. Shell and tube heat exchangers are known for their efficiency and versatility, making them suitable for various applications.
- Plate Heat Exchangers: These compact devices utilize thin plates to facilitate heat exchange between fluids. Their design allows for a large surface area in a small footprint, making them ideal for applications with space constraints.
- Air Coolers and Fin Fan Coolers: These systems use ambient air to cool fluids, making them energy-efficient and effective in various industrial settings.
- Finned Tube Heat Exchangers: Finned tubes feature extended surfaces and increase the heat transfer area, enhancing efficiency in heat exchange processes.
Importance of Heat Exchange Maintenance
Regular maintenance is essential to ensure the longevity and efficiency of custom radiator solutions. Heat exchange maintenance includes various activities such as heat exchanger cleaning, retubing, and hydrojetting.
- Heat Exchanger Cleaning: Over time, heat exchangers can accumulate deposits that hinder performance. Regular cleaning, including chemical and hydrojetting, helps maintain optimal heat transfer efficiency.
- Retubing: Retubing is a viable option in cases where tubes become corroded or damaged. This process replaces the damaged tubes, extending the life of the heat exchanger without the need for complete replacement.
- Bundle Puller: This tool simplifies the removal and replacement of heat exchanger bundles, making maintenance more efficient and less labor-intensive.
Custom radiator solutions can be designed and implemented to improve system performance…
The Role of Process Plant Turnarounds & InceptionIn industrial settings, process plant turnarounds are critical events that allow for thorough maintenance and upgrades. During these periods, custom radiator solutions can be designed and implemented to improve system performance. Inception phases during turnarounds provide an opportunity to assess existing systems and identify areas for improvement, ensuring that new installations meet the latest industry standards and operational requirements.
Benefits of Custom Radiator Solutions
- Enhanced Efficiency: Custom designs ensure that radiators and heat exchangers operate at peak efficiency, reducing energy consumption and operational costs.
- Reduced Downtime: Tailored solutions can lead to fewer breakdowns and maintenance needs, minimizing downtime and enhancing productivity.
- Improved Reliability: Custom radiators are designed to withstand specific operating conditions, resulting in more reliable performance over time.
- Longer Lifespan: By addressing the unique needs of each application, custom radiator solutions can extend the life of equipment, resulting in lower replacement costs.
Conclusion
In conclusion, the importance of custom radiator solutions in automotive and industrial applications cannot be overstated. With the ability to enhance efficiency, reduce downtime, and improve reliability, these tailored solutions are essential for modern operations. As industries continue to evolve, the demand for innovative and effective cooling solutions will only grow, making it imperative for manufacturers to invest in custom designs that meet the specific needs of their applications. By prioritizing heat exchanger manufacturing and maintenance, businesses can ensure optimal performance and longevity of their equipment, ultimately leading to greater success in their respective fields.